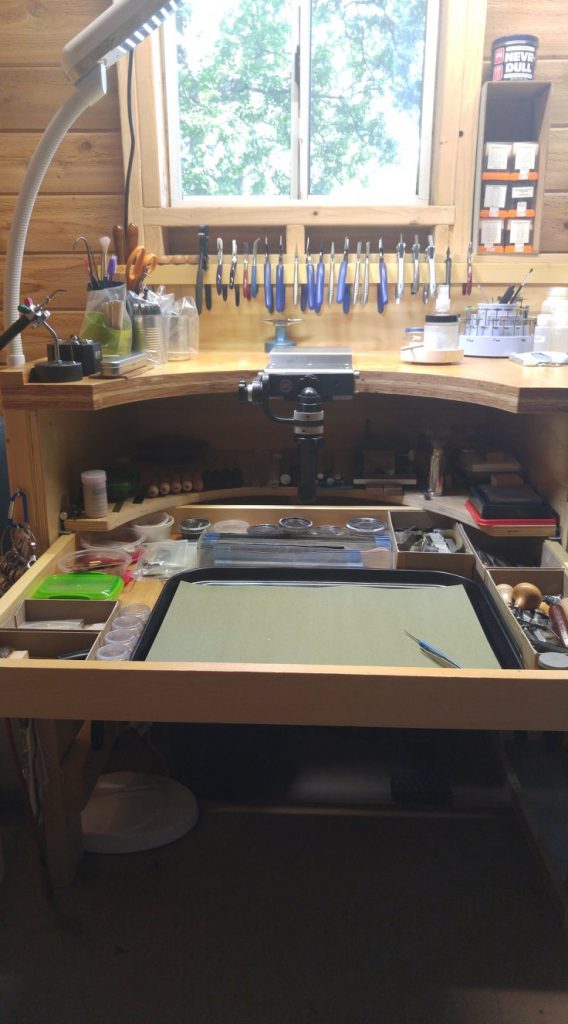
I needed to clean my bench, so I got busy and don’t think it’s been this clean and organized since Kathy and I built it three years ago! I really needed to organize my catch tray, as little pieces and strips of sand paper, unfinished projects, scraps and small tools mingled together don’t help when you’re trying to look for something.
Kathy made me five heavy-duty boxes out of some chipboard material that she uses in her album-making craft. They work perfectly to segregate tools, tweezers, sandpaper and other items, which will actually help me a LOT when it comes to finding something I need in a hurry, which usually happens when the torch is lit!
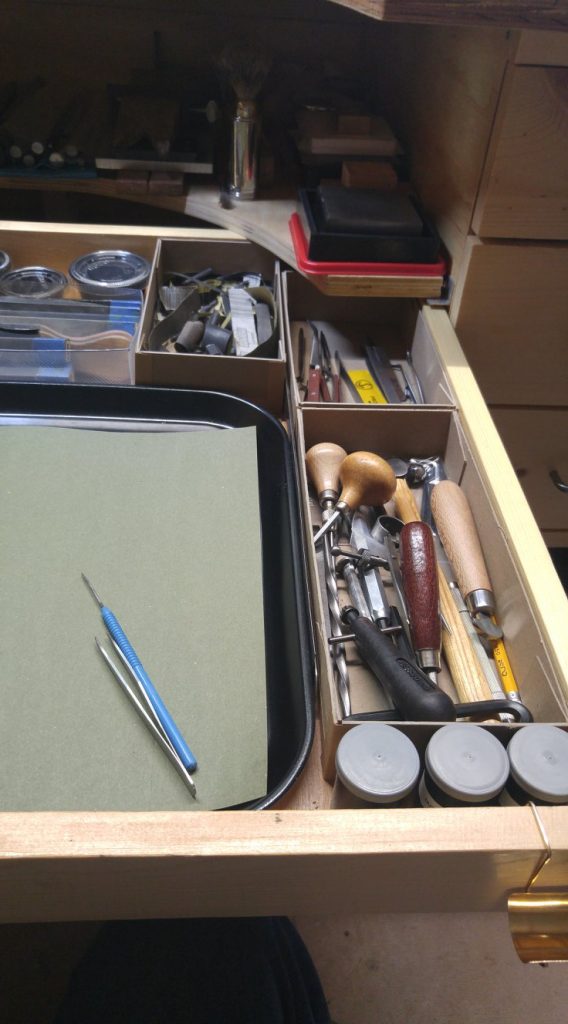
A couple of the smaller chipboard boxes Kathy made for my bench drawer…
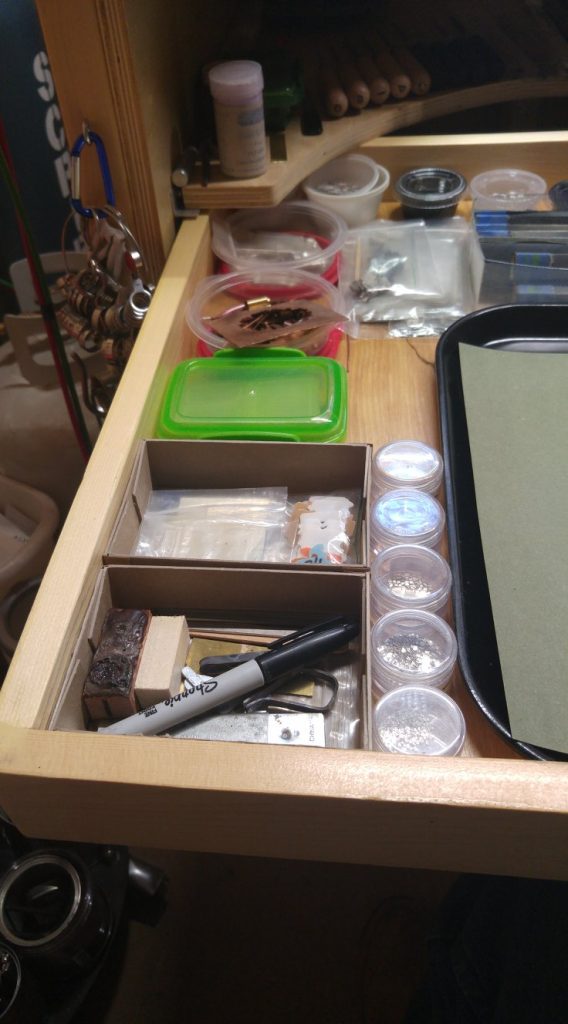
To celebrate the bench “makeover”, one of the things I did was to make a cradle for my flex shaft handpiece. I use a split mandrel on the flex shaft for sanding rings and jewelry all the time, changing out various grits of sandpaper strips on the mandrel as needed.
But, if you let the handpiece drop (it hangs vertically from its motor), the rolled strip falls off the mandrel easily and before you can use it again you have to pick it up off the floor, blow off the dirt and wrangle it back into the mandrel slot (a pain).
I used to open a drawer to set the handpiece on when I needed both hands for something, then later re-purposed a hook I had made from coat hanger wire for a portable torch set-up I have, but with just a hook it was always a balancing act (though better than having to open a drawer).
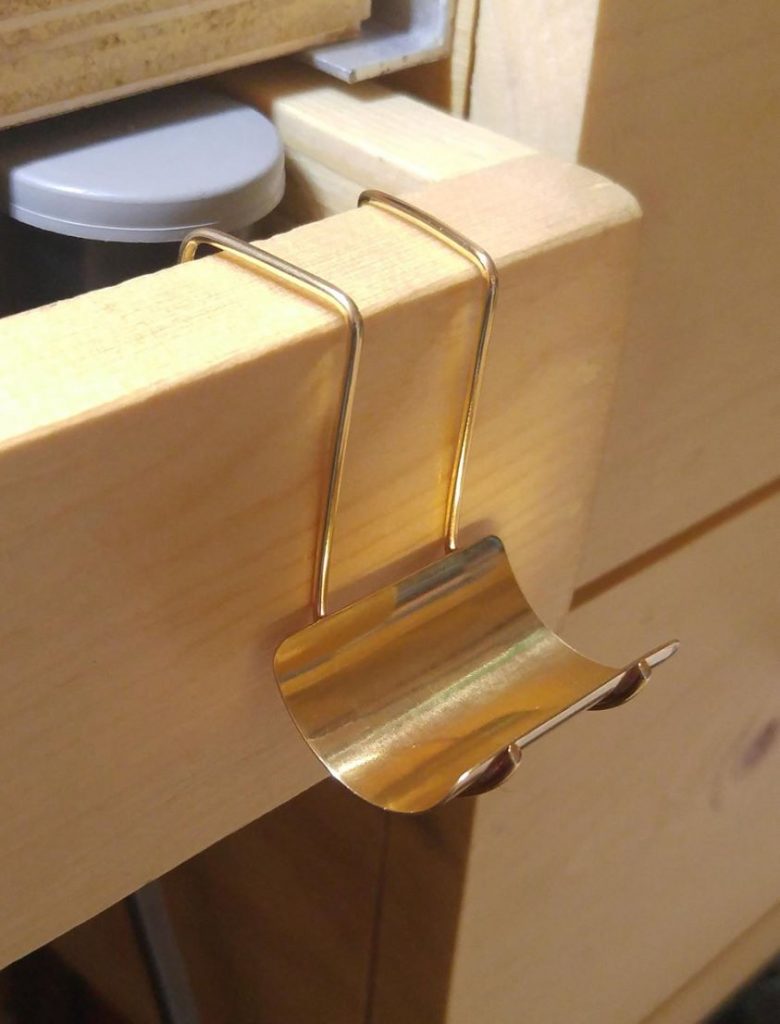
I only had 14 ga. brass wire on hand, so that’s what I used for the clip, soldering on a cradle cut from 24 ga. brass sheet and formed over the handle of a dapping die. After cleaning it up, I tumbled it for a couple hours in steel shot to harden the wire and give the clip the spring needed for proper tension, and it works great!
I now have a cradle for the handpiece so when I need to set it down for second, it’s right there close by, and holds it easily. No more having to pick up sandpaper rolls off the floor that fell out of the mandrel!
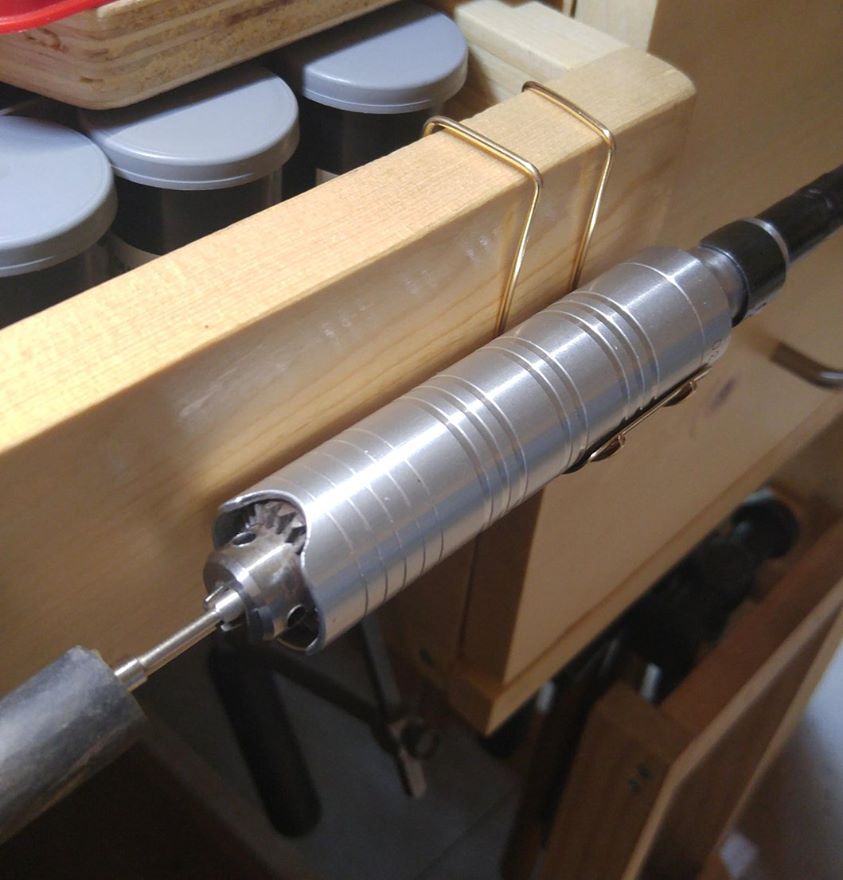