Below is a piece of yellow Cubic Zirconia (CZ) cut and faceted in the “Graham Portuguese” design by Jeff R. Graham, weighing in at 13.50 carats and 11.75 mm diameter.
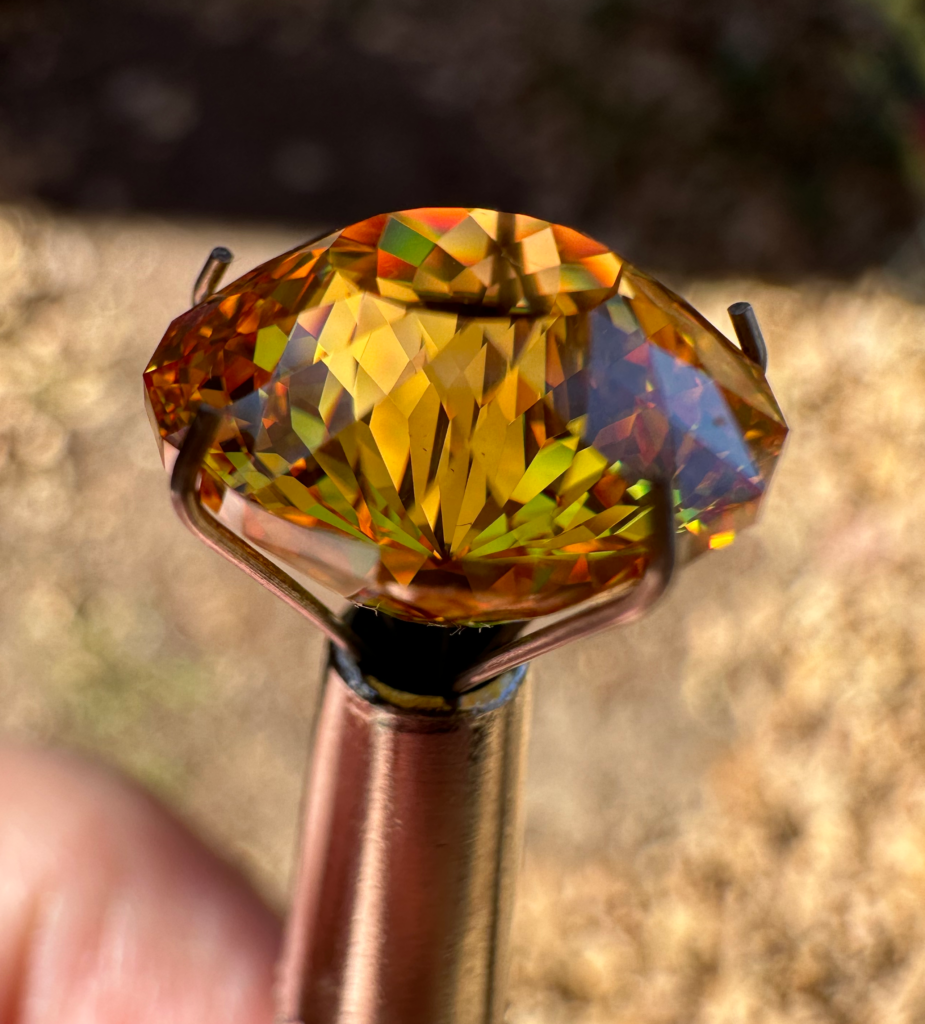
The traditional “Portuguese” cut has been around for a very long time and has been cut by numerous faceters around the world, but Jeff Graham improved on the design in 2002, revising it especially for gems with refractive indexes between 1.76 (Sapphires and Rubies) and 2.14 (Phosgenite and Mimetite), which would include many Garnets (1.77-2.02) and Zircons (1.81-2.02) . With the refractive index for Cubic Zirconia being so close at 2.15-2.18, the improved design cut using that material would really enhance it, too.
Mr. Graham mentioned in his Cutting Remarks included with the design that “YAG*, CZ, and man-made Sapphire are all good materials for this design” and suggested “a light colored material and obviously larger stone”, so yellow CZ it was. There are 161 facets on this stone (including the girdle), so this stone sets a new personal record for the most facets on a single stone that I’ve done to date.
*YAG: Yttrium Aluminium Garnet, a synthetic material developed for use in optics and lasers, but also provides a good faceting material alternative.
I was beginning to have a love/hate relationship with CZ, at least with this particular piece. I love CZ in that, being a synthetic lab-created stone, it makes for some very inexpensive material to facet with. I purchased two kilos of the stuff a couple years ago comprised of six different colors for $80, shipping included. That equates to a cost of less than $0.01/carat ($0.00814/carat to be exact). Two kilos sounds like a lot of Cubic Zirconia, but it is some very heavy stuff… you could easily substitute fishing weights of CZ with those of the same size in lead I think, it’s that heavy. But, I wanted some very inexpensive material that I could learn to facet with, and CZ fit the bill nicely.
After the chunks of material arrived from overseas they were cut up on my trim saw, and a good number of pieces roughly pre-formed on my cabbing machine while I anxiously waited for my faceting machine to arrive. I estimate that it likely cost me about $0.02/carat after taking into account what was lost in the sawing and pre-forming process, which still makes it very inexpensive material to facet. This piece for example (which which looks like a lemon gum drop), weighed in at 42.95 carats pre-formed and cost me $0.86 at that rate. What’s not to love about that?
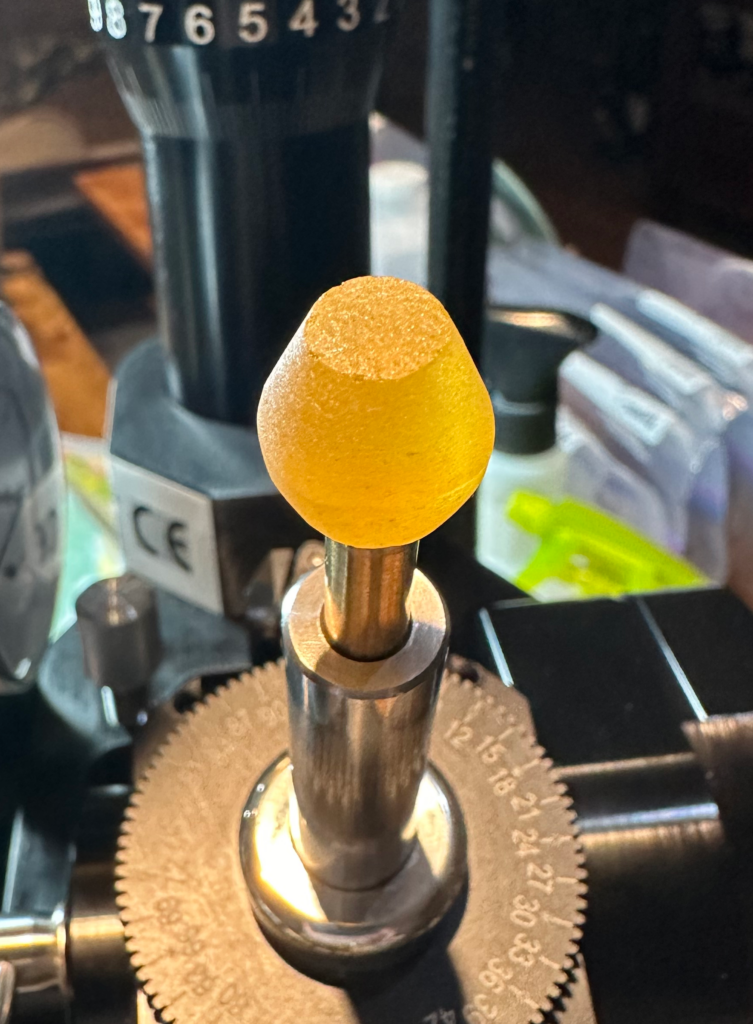
Once Cubic Zirconia is faceted, it really does have some of the most “bling” of any stone I’ve seen, with flashes of color that even diamonds can’t mimic. Diamonds reflect more pure white light, whereas CZ, due to its excessive light dispersion, reflects a much more noticeable rainbow-colored light and is one of the ways you can actually tell the difference between the two. It’s not near as hard as diamonds either, coming in on the Mohs scale even behind corundum (Sapphires and Rubies) at 8.5.
My “hate” relationship with this particular stone however was due to just how easy (and constant) it got scratches when working the pavilion. Scratches are a part of faceting and cabbing, literally. You start out removing stone by scratching it away, and then subsequently remove those scratches with finer and finer material until you seemingly remove the visible scratches, leaving behind a mirror polish. If you were to look at that mirror finish under a high-powered micron-scope, the scratches are still there, but just so tiny so they can’t be seen with the naked eye (or even a jeweler’s loupe). So in reality, you didn’t “polish away” the scratches, you just made them too small to see. 😉
However, when faceting stones, sometimes a piece of the material will just dislodge itself from the facet you’re working on and leave a scratch on your nicely faceted plane as it grates across the surface. Quartz is known for this trait, and my first thoughts on this piece of CZ was that it was putting Quartz to shame. Not only did I have to use an extremely light touch when faceting the pavilion, but I also had to drop the RPMs on the machine down to about 250 on the pre-polish and polish grits (I normally pre-polish anywhere from 300-600 RPM, and polish at about 300-500 RPM).
I also had to take it all the way through from the 3K, to the 14K and finally 60K diamond grits to get it polished, and even then I still had a couple facets that I just could not completely clear of a scratch (or I would have over-polished that facet and ruined the meet-point). The scratches might not be visible to most with just the naked eye, but they can definitely be seen with a 10x loupe, however I preferred that trade-off over sloppy meet-points which I think are more readily noticeable.
Combine a SLOW lap with needing an extremely light touch and having to progress though three different grits just to get a polish takes a lot of patience, but when you have your facet almost completely polished and then suddenly a scratch appears across its surface, it’s not only frustrating but even more time-consuming. You have to stop and clean the gem and lap of all diamond compound and swarf (the “mud” that is created from the diamond grit, oil and particles of the gemstone that are removed during the faceting process). If you don’t, you might have the culprit that caused that first scratch connect with your stone again and cause another! 😱
I didn’t recall having had this problem with the other CZ stones I’ve faceted, as three of my first four stones I ever faceted were in CZ (and one of those in this same yellow material). I think if I had, I may have given up faceting before I even got started! Seriously though, working the pavilion on this stone certainly tested my patience. If I didn’t enjoy the craft so much, I think I might have just thrown this one in my tackle box, willing it to be snagged and lost in the murky depths at the bottom of some pond or lake and chosen another stone to work on. Don’t think the thought didn’t cross my mind!
Here’s a shot of that lemon gum drop now, with the pavilion and girdle facets completed. There are 96 facets cut so far (16 for the girdle, and five tiers on the pavilion, each with 16 facets as well). The rough stone was formed on a 320 grit lap followed by a 600 grit lap for the girdle and first tier to establish a center point, but the other tiers, due to the decreasing size of the facets, were cut when working the stone on the 1,200 and 3,000 grit laps, followed by the 14,000 and 60,000 grit pre-polish and polish laps. That calculates to having worked each facet between 4-6 times, for a combined total of 448 facets worked (so far). Whew!
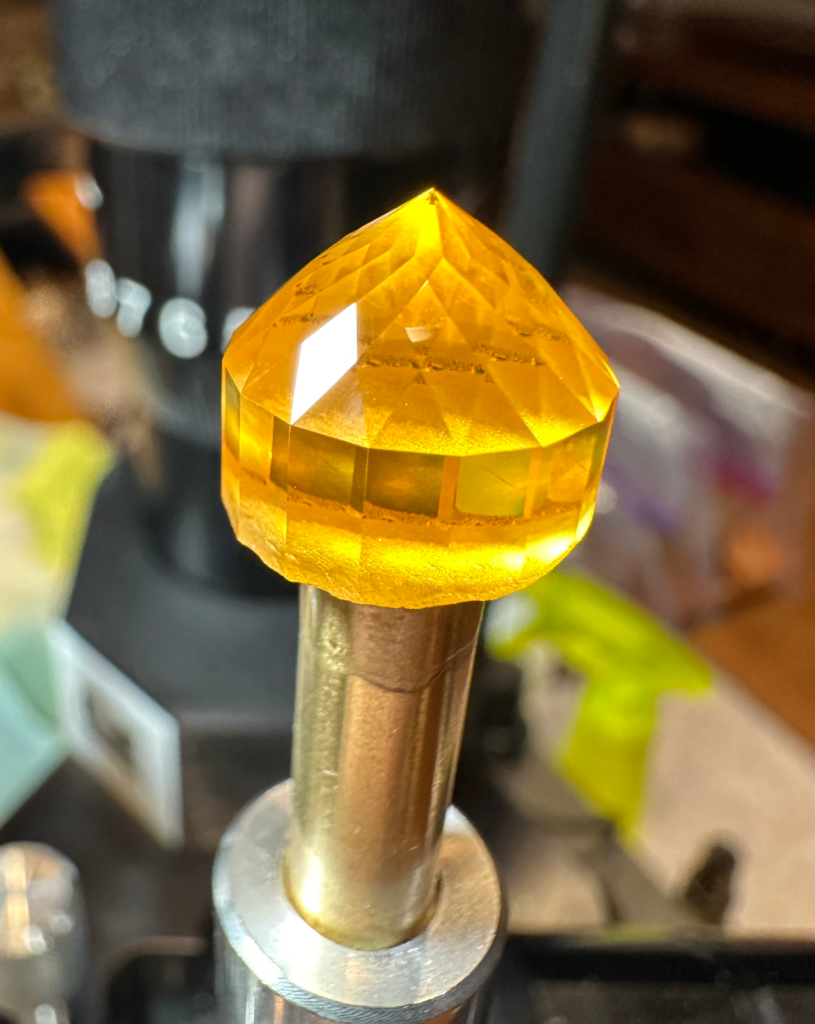
After transferring the stone to the another dop to work the crown and stepping through the 320, 1,200 and 3,000 grit topper laps to get those facets in place, I decided to stop and thoroughly clean the splash pan that the laps spin in, wipe down the spindle, gears, mast and generally the entire machine.
I usually clean up the machine after faceting a stone before moving on to faceting another, but I was wondering if perhaps some of the fine CZ dust clinging to the splash pan or equipment after cutting down the stone on the courser 320-3000 grit laps was getting knocked or blown loose, and that dust may have played a role in all the scratches I was getting on the pavilion.
That appeared to have done the trick, as I was able to work the crown without the frustration and hassle that I was experiencing with numerous scratches suddenly appearing on facets I was polishing on the pavilion, which was a tremendous relief! I was able to proceed straight to the 8,000 pre-polish and 60,000 polish grits, saving myself the time in having to work the facets on the 14,000 grit lap, and all with the regular minor scratch to remove here or there as usually incurred while faceting.
There are four tiers on the crown, again with 16 facets per tier, for a total of 64 facets (not including the table), and already this gem is sparkling and flashing every color in the rainbow (which CZ is so well known for), even without the table having been cut yet…

The color of the gem looks a little different from previous pics as I moved the printer cart that the faceting machine is seated on out of the living room to another area (had to make room for our Christmas tree!), so the different lighting is the reason it looks less bright lemon-color and more golden.
Here is a side-view shot of the completed gem showing the numerous facets on the pavilion and crown, which makes for a very flashy gem no mater what material it’s cut in practically, but especially when Cubic Zirconia is used.
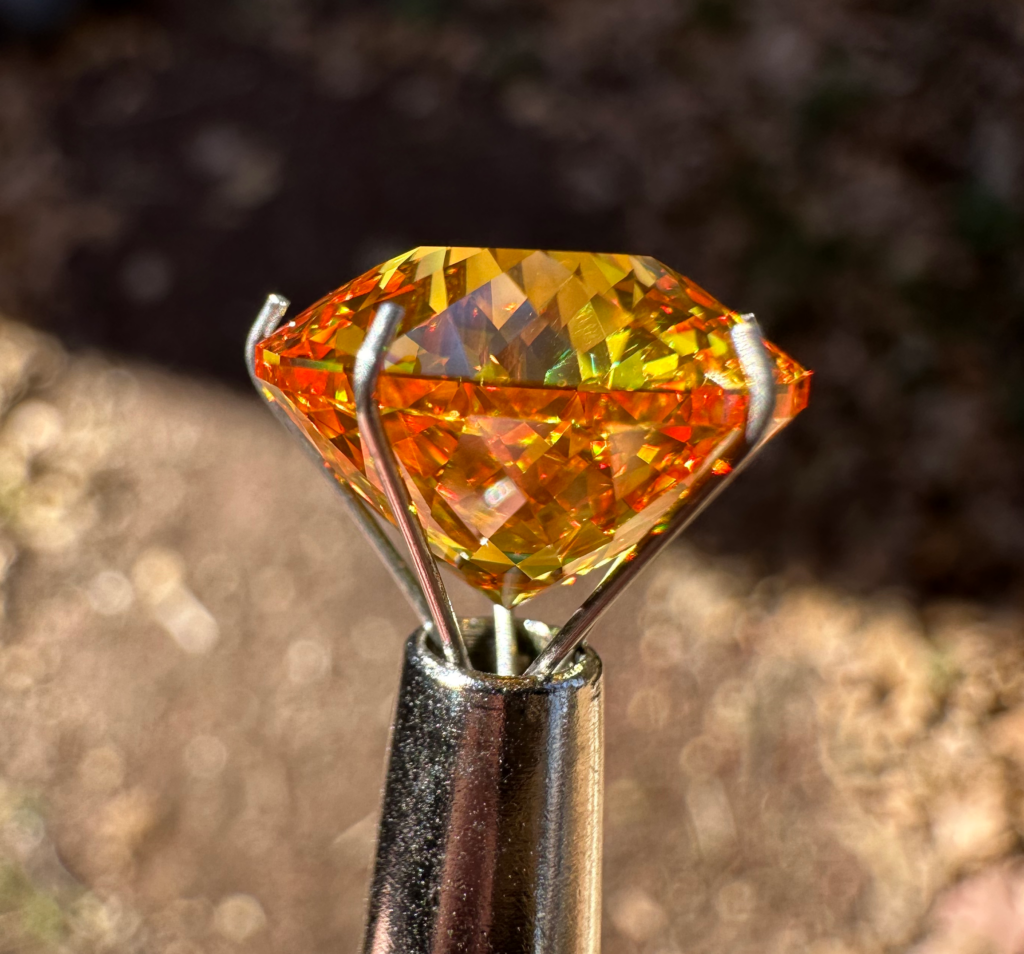
Cutting the “Graham Portuguese” design with its 161 facets was certainly a challenge, and this piece did try my patience getting the pavilion cut, but it definitely won’t be the last gem I cut in this design. Overall it’s not a difficult gem design to cut, just tedious as each tier has 16 facets and the indices alternate between tiers, so really the only thing that changes is the angle the tiers are cut at.
With all the work that went into it, and the fact that it actually did turn out very well in the end, I guess it won’t be relegated to the tackle box after all. 😉