Now that I’ve worked with the CabKing 6″ cabbing machine for a few months, I figured I would give it a review of sorts. There are several companies that make quality cabbing equipment, and CabKing is one of them. Although I’m no expert on cabbing machines by any stretch, so far this machine has operated flawlessly and I’ve thoroughly enjoyed using the CabKing machine to cab stones. I have been able to inspect every detail, work with its operation and use the accessories that come with it, and can at least offer my thoughts on the CabKing 6″ and its operation.
First, the 1/4 HP, 1,800 RPM direct drive motor on the 6″ machine has absolutely no problem spinning the wheels and discs attached, and runs extremely smooth and quiet. The motor actually runs as quiet or quieter than the motor of a polishing unit I use on jewelry. That unit also has a blower to filter the air and polishing compound coming off the wheels that I always have turned on (and makes most of the noise on that machine). So, depending on what grinding wheel I’m using on the cabbing machine, the jewelry polisher can be even louder at times. Actually, the water pump makes the most noise of all I think, but it too does its job very well.
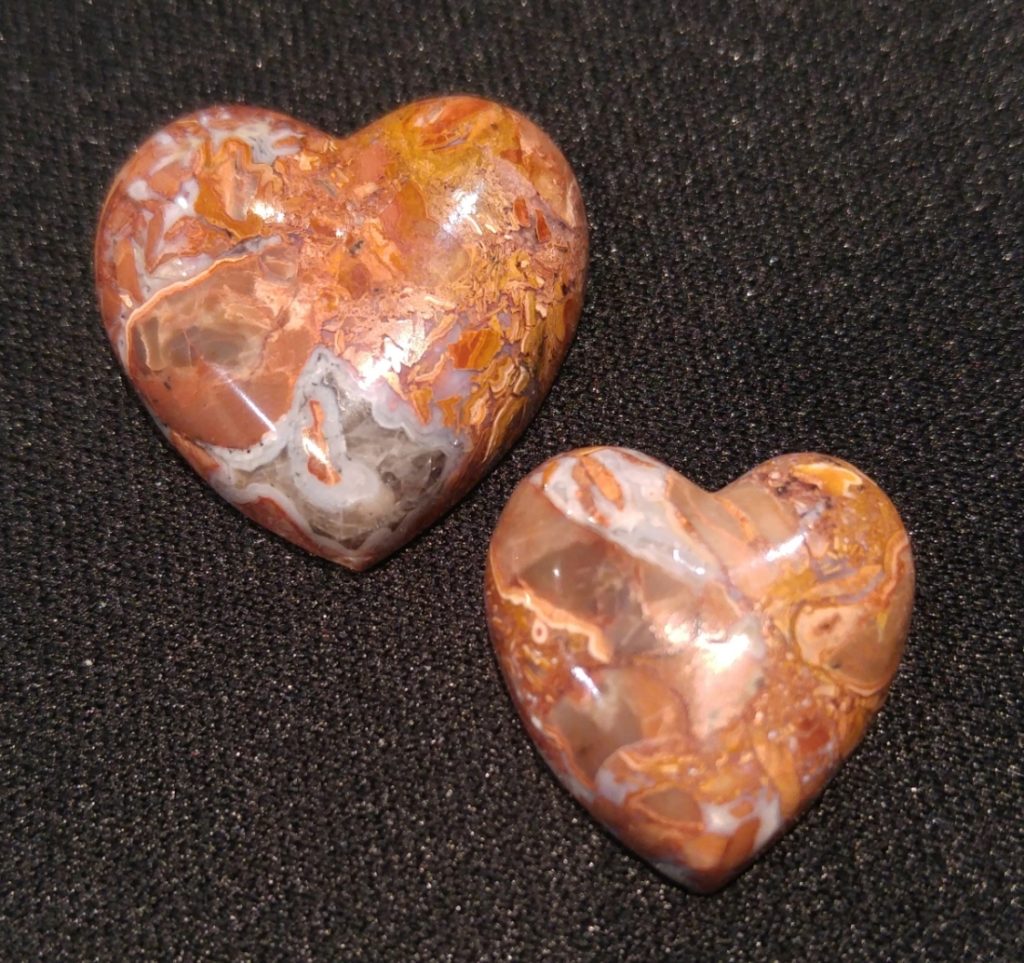
“…cabbing the occasional large stone, heart or window on a piece that needs the extra spacing is something that can certainly be done on the 6″ machine without much trouble at all.”
In researching cabbing machines before I settled on the CabKing 6”, I had read where some feel a 1/4 HP motor isn’t efficient for driving six wheels on a cabbing machine, and the user might experience a slow-down of the motor when pressing the stone against the wheel or disc. I found absolutely no proof of that on the CabKing 6″ machine.
I certainly haven’t experienced any slowing down of the motor at all, even when pressing much harder against the wheels than necessary. I think a large part of that theory with some may be more for machines using Silicon Carbide wheels/discs perhaps. With diamond wheels and discs the diamond usually does the work very effectively and there is no need to press the stone against the wheel or disc hard at all. In fact, pressing too hard only decreases the life of the diamond wheel/disc by dislodging the grit embedded in the electroplating or resin, and they won’t cut the stone any faster, either.
The motor does get very hot (there’s even a warning label on it to not touch the motor housing when it’s been running), but since it’s out of the way of any working areas, and that is considered normal operation, there’s not really a problem with it that I can see.
Some may fault the CabKing 6″ machine when compared to their 8″ machine as not being as “robust”, which is somewhat true to an extent. The 8″ machine has larger wheels and a more powerful motor, but is also quite a bit more expensive as well (almost double the price). The wheels on the 8″ machine are spaced further apart, allowing for more room between wheels for working with larger stones, or cabbing hearts and other designs where you need room to work on the edge of the wheels, but unless working with larger material or cabbing those designs is frequently done, the 6″ machine will do everything the 8″ machine can do. It just might take a bit longer, having to remove a wheel and use spacers to give you that room, swapping out wheels as needed.
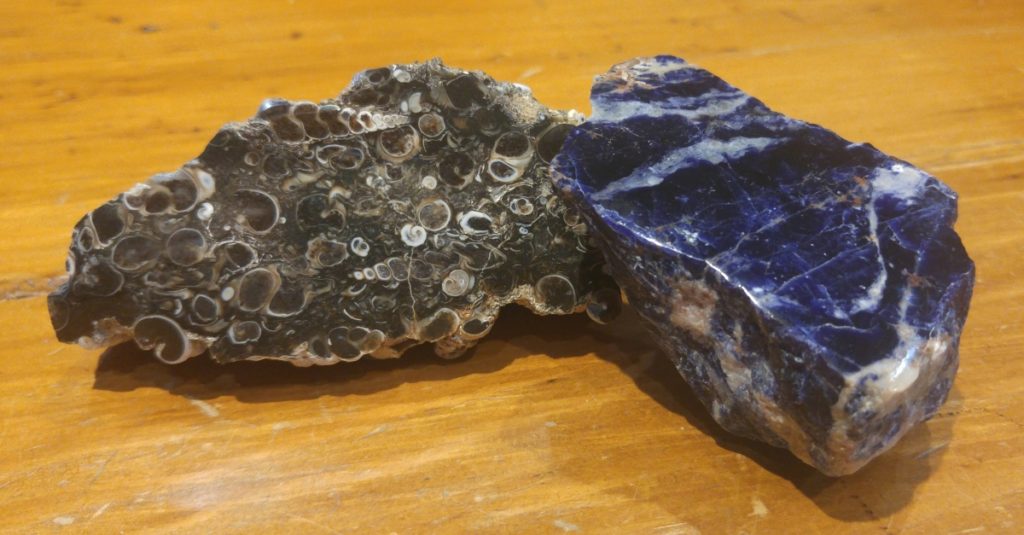
If the overall durability of both machines is on par with each other, aside from larger wheels with more spacing between them, and a 3/4 HP motor instead of a 1/4 HP motor, the only real difference between the 6″ and 8″ packages is that two sets of resin diamond wheels are provided with the 8″ machine whereas a single set is provided with the 6″ machine, and a foot switch to power on/off the water pump. As quality resin wheels usually last for many, many stones, if CabKing didn’t include a second set of wheels with their 8″ machine the price could likely be dropped by about $400 (which can be a lot when budgeting for a new machine).
If there is a need to cab stones that are too large or of a shape that can’t be worked with the more narrow wheel spacing on the 6″ machine, they can be accommodated by removing a wheel and using the extra supplied wheel spacers in its place. Swapping out wheels with spacers takes a little time (though not much, really), but cabbing the occasional large stone, heart or window on a piece that needs the extra spacing is something that can certainly be done on the 6″ machine without much trouble at all.
There are plenty of businesses that use the 6″ machines in their work on a daily bases, cabbing hundreds of stones a day for production (attesting to their durability). The 8″ wheels may cost less in the long run with regards to wear by having a larger surface area, but the tighter radius of the 6″ wheels can allow for less material waste on small stones, especially those such as turquoise which are usually cabbed free-form to conserve as much stone as possible.
One of the features I like best about the CabKing cabbing machines is that the water supplied to the grinding wheels and laps to keep them wet, the stones cool and wash away the swarf is not recycled water sitting in the tray full of rock mud delivered by bubblers, but fresh, clean water delivered from a water pump out of a bucket or container. This not only keeps contamination from particles that could cause unwanted scratches low, but also greatly decreases the amount of rock particles (such as silica) residing in water spray or mist coming off the wheels from entering the air and posing a health risk. Control knobs for each wheel and end-lap allow for precisely managing the water flow, from a trickle to steady stream.
Another feature I like about the CabKing cabbing machines (though many other companies include this as well), is the ability to use polishing and diamond flat lap discs on the end of the wheel shafts of each arbor. By using a polishing disc on the end of the wheels, the cost of having to purchase a separate polishing unit to complete the cabbing process is saved. The polishing discs spin at speedy 1,800 RPM since the machine doesn’t have variable speed, which is fast for polishing some stones (especially if heat-sensitive), but taking it slow and working more in the center of the disc hasn’t been an issue (at least not yet… anything can happen).
Right along with polishing discs are diamond flat laps. A 360-grit diamond lap comes with the unit, which is great for ensuring flat bottoms on rough stones. Other grits of diamond laps are widely available, allowing for grinding and polishing flat surfaces through every stage. This is an added plus for rock collectors, allowing “windows” to be ground and polished on select stone and mineral samples, often greatly enhancing their appearance.
For those on a tight budget, CabKing also makes a trim saw attachment for their machines. By removing the wheel housing on the right-hand side of the machine along with the three wheels mounted (which slides off the arbor as one piece, wheels attached), it can be easily swapped out with an arbor sleeve having an 8″ trim saw blade. A base with tray, cutting surfaces and splash shield for the blade are included, making the unit even more effective as an “all-in-one” machine for trimming rough rock and slabs (or cutting small slabs) as well as any grinding and polishing needed to get a stone to its final finish.
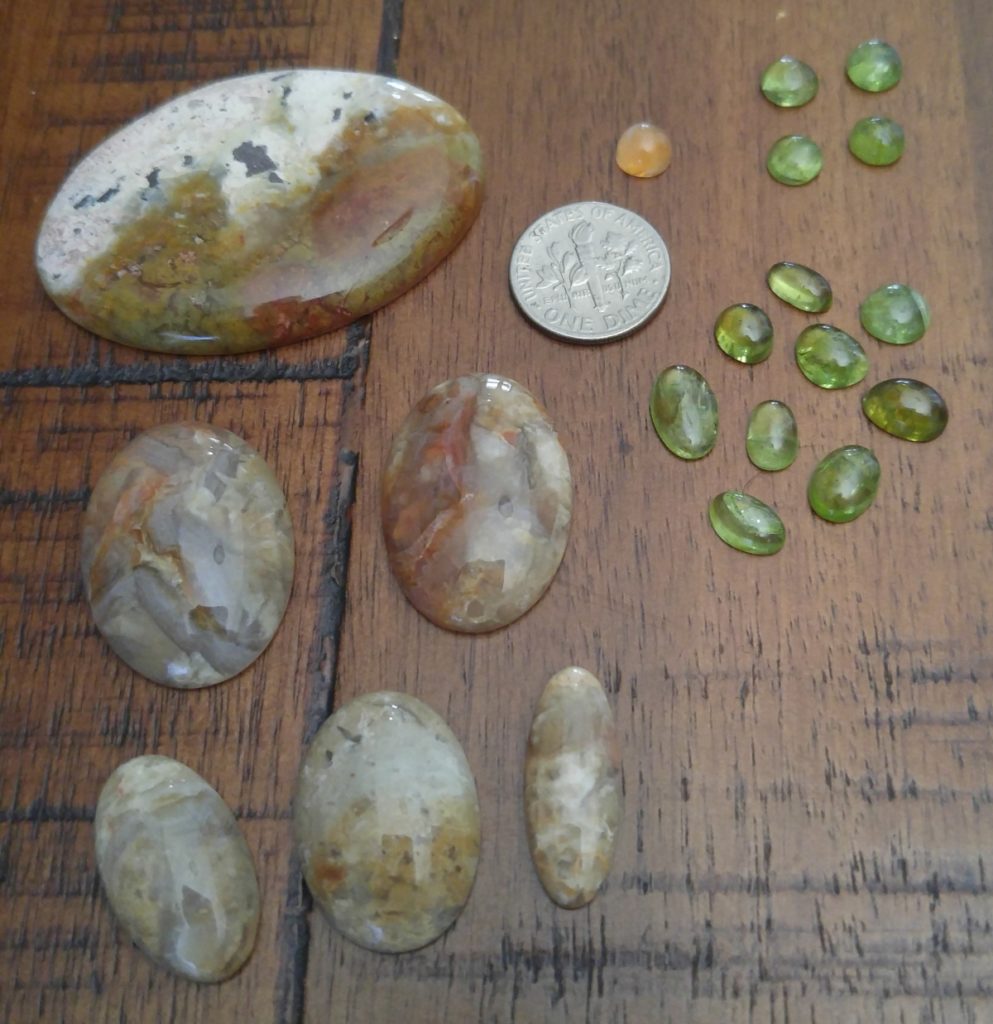
Overall, I’m extremely pleased with the quality, durability and operation that the CabKing 6” cabbing machine has shown, and expect it to last for many,, many years. The only parts that would need replacement on occasion (aside from the wheels and discs, which is expected with any machine) would be the 1/2″ drainage tubing for the trays, or the 1/8″ water feed tubing. The drainage tubing is rather thin to be more flexible, but both are standard tubing sizes that can be bought at just about any hardware store if needed. The other parts of the water feed system are durable plastic that can be easily cleaned with a pipe cleaner (CabKing even supplies one of those!), so other than normal cleaning and maintenance, the machine is built to last.
If you’ve made it this far, I thank you for visiting and reading this review. I feel the CabKing 6″ cabbing machine was a solid purchase of quality equipment that will allow me create quality cabochons, as both a hobby or business, now and far into the future.